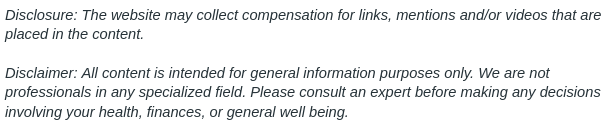

Quite simply, packaging machines carry out the process of attractively presenting a product in a package with labeling that spurs people on to purchase what the manufacturer is selling. Packaging also includes instructions about ingredients, and nutrients, if fitting, as well as how to use the product and how to dispose of it.
There are different types of packaging machines that do particular jobs along the packaging process. Some of these are pouch filling machines, food metal detectors, sealing machines, checkweigher machines, and more.
Great care is taken in the inspection of foods before, during, and after they are sent through packaging machines and offered to the public for consumption. Examination is very thorough of all food items as part of the packaging process. Food metal detectors are used to examine foods inside and out for any hard to see or microscopic pieces of metal that could be harmful to customers.
Food metal detectors are packaging machines that can be added to every step of the packaging process in order to conduct the most exhaustive inspection possible. Tiny grains or specks of metal could accidentally enter the item during packaging and these could be a major health hazard if eaten. Repercussions of this type of incident would be, without a doubt, serious, and far reaching. Not only could serious damage be done to the customer, but the manufacturer could face tremendous financial loss due to resulting law suits and product recall. The three main types of foreign metal that can be recognized by a food metal detector are stainless steel, and ferrous and non-ferrous contaminants.
Foodborne diseases can have the same results if even one individual eats a product that, unknown to the manufacturer, carries an illness that could be harmful when consumed. Statistics show that every year approximately 48 million people suffer some kind of disease that is caused by eating contaminated food. About 128,000 seek medical help and spend time in a hospital. Unfortunately, approximately 3,000 people suffer loss of life as a result.
Vacuum sealers, often part of the packaging process, are known to keep foods fresh up to five times longer than when the food simply sits in a container or a plastic bag. This type of packaging is the process by which air is removed from the package before it is sealed. Vacuum sealing can be done either automatically or manually, and is done by placing the product inside a package made of plastic film, removing the air, and then sealing it. Using this method, the shelf life of foods is extended, and, because the packaging is flexible and the air is removed, it reduces the volume of the package. In addition, because there is no air inside the package, the risk of the growth of any type of bacteria is greatly reduced.
Other items that can be vacuum packed are clothing and bedding. This type of packaging can even be done at home by inserting a vacuum cleaner hose into the opening of a specially designed bag in order to remove the air from inside the package. The size of the bag will become much smaller and the bags can even be stacked or stored in spaces where they would not normally be able to fit.
Vertical form fill and seal is another type of packaging that is good for many kinds of products such as cheese, frozen foods, coffee, powders, seafoods, chocolate, meat, poultry, and much more. This process begins with a roll of film in the shape of a cylinder which is pulled through a vertical bagging machine. The machine brings the film through a tube, after which the film is folded into bag shape and will be sealed by vertical seal bars. The folded film is now in a pouch like form. The bag is then filled with the product, after which the length of the pouch is sealed. The finished package will have top and bottom horizontal seals and one vertical seal across the back.
How a package is sealed has an impact on the environment. Professionals in the packaging business believe that every single plastic package has the potential to eliminate at least 1.7 pounds of food waste.